Blogs
October 24, 2024Developments in the olefins value chain
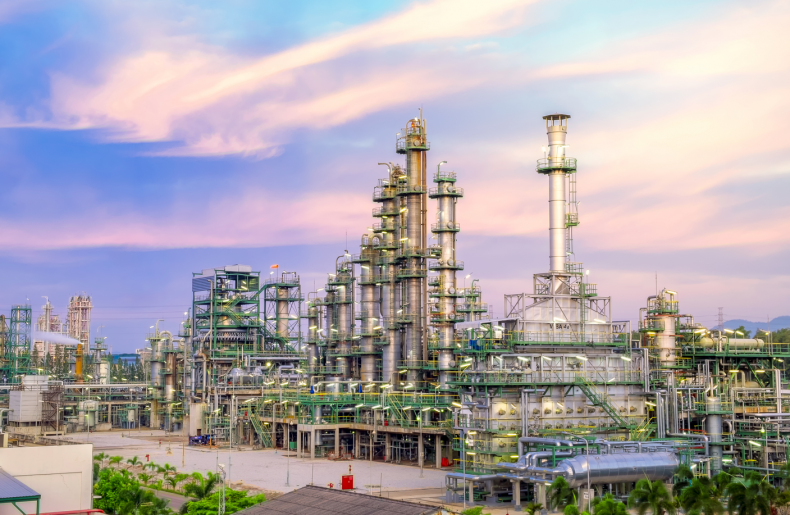
The most commercially important olefins are ethylene, propylene and butadiene. The ethylene market continued to buckle under heavy capacity addition and relatively weak demand growth in 2023, but a mild recovery in demand is underway in 2024.
A variety of feedstocks are used for olefins production, most of which are produced from the refining of crude oil or the processing of natural gas. The availability of coal and methane at low prices in some regions have driven technology development to exploit alternative process routes utilising these feeds in favour of higher priced conventional petrochemical feedstocks. The spike in Chinese coal prices in recent years, and the high emissions have however deterred more investment in coal chemicals. In addition, the increasing focus on decarbonisation favours lighter feeds, and several regions are developing carbon sequestration infrastructure to support new cracker projects.
The world generates an estimated 2 billion tons of municipal solid waste (MSW) , with a third not being managed properly. Global waste is forecast to grow to 3.4 billion tons by 2050, more than doubling population growth during that time frame. The quantity of waste in low-income countries is forecast to triple by 2050. The East Asian and Pacific region is generating the most of the world’s waste, currently estimated at 23 percent. Close to 45 percent of the global waste stream was comprised of food and green (or organic) waste. At the same time, dry recyclables such as paper and cardboard, plastics, metal, and glass represented close to 40 percent worldwide.
There are currently well over one hundred companies developing technologies to break down plastic waste into basic hydrocarbons which can be used either as fuels or petrochemical feedstock. Although the petrochemicals industry will compete with the sustainable fuels business for both plastic and bio-derived feedstocks. High oil prices greatly favour renewable or bio-based feedstocks, although the merits of use in olefins production versus other purposes has yet to be fully established.
Most processes are based around pyrolysis – heating the plastics in an oxygen-free atmosphere until the polymers break down into basic hydrocarbons which can be refined for use as fuels or steam cracker feedstock. Other processes using e.g. supercritical water are also being implemented at scale. Chemical recycling is inherently less desirable than mechanical recycling, as the costs and energy consumption are higher, and the basic hydrocarbons produced have a much lower value than recycled polymers. Chemical/pyrolytic recycling is however a potentially attractive way of handling low value waste streams such as post-consumer polyolefin films and mixed plastics which cannot be mechanically recycled.
Pyrolysis has been touted as a “last resort” recycling process which could consume plastic waste streams which are too contaminated for either mechanical or chemical recycling processes. The experience to date however illustrates that the processes are very difficult to operate, and as a result, quite sensitive in terms of the waste stream they can process. The commercialisation of larger scale units will doubtless avoid some of the problems encountered on the demonstration plants, but further difficulties are expected in ramping-up production at the pyrolysis plants. A new industry is also taking shape to upgrade the raw pyrolysis oils into optimal cracker feedstocks. Processes need to remove contaminants such as halogens but will also require large quantities of hydrogen to provide lighter molecules which have a greater circularity towards light olefins than heavy feedstocks.
There is no particular economic or environmental merit in using these hydrocarbons for petrochemical use instead of fuels, although in doing so the system functions like EPR, and the polymer producers are thus responsible for handling these often expensive and low purity products. Governments and regulatory authorities have been very cautious regarding chemical recycling, with neither the U.S. federal authorities nor the European Commission currently classing it as “recycling”. Several U.S. states have however independently approved it. The situation appears finely balanced, although the bold moves such as the target of a minimum 30 percent recycled content in packaging which now has the support of the industry bodies in Europe and the United States is expected to be reciprocated with some recognition of chemical recycling. In Europe, recognition by the European Commission would make plastic waste recycled in this way deductible from the non-recycled plastic waste totals which nation states now need to pay a levy of €800 per ton. The consensus expectation currently is that mass balance accounting would not include the proportion of the recycled feedstock which exits the recycling and cracking process as fuels (fuels-exempt). This means that this fuel proportion of the pyrolysis oil would be sold at the relatively low fuels price, and a smaller proportion could be designated as higher value circular polymers. While chemical recycling does not fulfil all the economic objectives and has higher associated carbon emissions than mechanical recycling, it does have the economic benefit of reducing Europe’s crude oil imports.
Impact of Polymers Circularity
Polyolefins demand is the key driver for olefins production; around sixty percent of ethylene is used in polyethylene production, while around seventy percent of propylene is used in polypropylene production. The focus on circularity however suggests that more plastic-derived products will flow back into olefins production to produce circular polymers, while more bio-origin hydrocarbons will continue to be used as fuels.
Reduce and reuse are best approaches to minimize environmental impact of plastics waste, followed by mechanical recycling including solvolysis. Depolymerisation retain monomer structure are comparable to mechanical recycling in terms of environmental benefits; Pyrolysis/gasification, consume a considerable amount of energy and offer lower CO2 reductions, although mixed plastics waste can be tolerated; Energy recovery by incineration generates significant CO2 that needs to be captured.
Circular Plastics Value Chain
Global demand for all polyolefins was 207 million tons in 2023, an increase of nearly 3 percent from 2022. The global economy continued to struggle with inflationary and cost-of-living pressures through 2023, although these problems eased, and growth resumed progressively into 2024.
Find out more...
Market Analytics: Olefins Feedstocks - 2024
This report provides a detailed analysis of the regional feedstock requirements for olefin production - ethylene, propylene and butadiene - including forecasts to 2050. Feedstocks include naphtha, methanol, ethanol, ethane, propane, butane, and gas oil.In addition, this report now includes discussion and forecasts of the development of recycled 'plastic oil' as a cracker feedstock.
Market Analytics: Olefins - 2024
This report provides analysis and forecasts to 2050 of supply and demand of the global olefins market. This analysis identifies the issues shaping the olefins industry as well as provide detailed demand breakdown by derivative, supply and net trade data for 40 countries.
Market Analytics: Polyolefins - 2024
This report provides analysis and forecasts to 2050 of supply and demand of the global polyolefins markets, including low density polyethylene (LDPE), linear low density polyethylene (LLDPE), high density polyethylene (HDPE) and polypropylene. This analysis identifies the issues shaping the industry as well as provide detailed demand breakdown by end-use and supply, demand and net trade data for 40 countries.
Recycling Options for Polyolefins (2023 Program)
This report begins by defining polyolefins, followed by an overview of production technology pertinent to polyolefins. It then highlights recent business advancements for each polymer grade, along with providing a list of technology licensors and developers. The report will then delve into a comprehensive analysis of four pivotal recycling technologies — mechanical recycling, solvent-based purification, pyrolysis, and hydrothermal treatment — that are either under development or being commercialized for the recycling and valorization of polyolefin waste.
Packaging Design for Recyclability and Cost (2023 Program)
Providing an extensive analysis of packaging design for recyclability, examining the mechanics and economics of blown film extrusion, cast film extrusion, bi-axially oriented film extrusion, and thermoforming across three key regions: the United States Gulf Coast (USGC), Western Europe, and China, referencing Q2 2023 pricing data. The report delves into the carbon intensity of these processes measured in tons of CO2 equivalent per ton of produced material.
Biorenewable Insights: Bio-naphtha as a Chemical Feedstock (2020 Program)
This report analyzes the technoeconomic developments in bio-naphtha technologies. Commercial hydroprocessed esters and fatty acids (HEFA), Fischer-Tropsch (FT), and pyrolysis based processes and high level economics are presented. Upcoming biorefining project (that include bio-naphtha units) are analyzed. Impacts on the conventional industry, trends and drivers are also discussed.
About Us - NexantECA, the Energy and Chemicals Advisory company is the leading advisor to the energy, refining, and chemical industries. Our clientele ranges from major oil and chemical companies, governments, investors, and financial institutions to regulators, development agencies, and law firms. Using a combination of business and technical expertise, with deep and broad understanding of markets, technologies and economics, NexantECA provides solutions that our clients have relied upon for over 50 years.