Blogs
September 17, 2024Bio-Butadiene: Interest is bouncing back
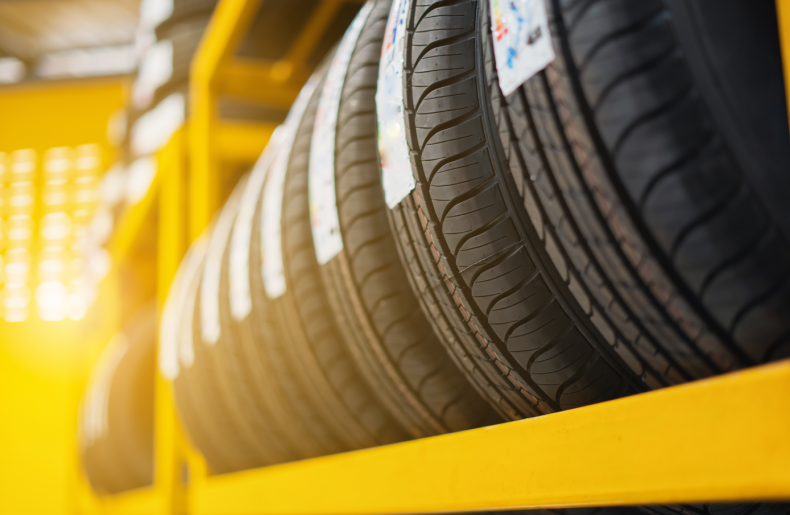
Background
Recent developments have resulted in a tightening of the butadiene markets, particularly with deficits observed in C4 crude in regions like North America. Additionally, spikes in energy prices have negatively impacted European cracker economics, resulting in reduced production of both ethylene and butadiene. While the tightening of butadiene markets is favorable for the commercialization of bio-butadiene, the higher production costs pose challenges in terms of competitiveness when compared to current market prices. Presently, the supply of steam cracker crude C4 exceeds the forecasted butadiene consumption. However, in Europe, a shift towards lighter feedstock and the establishment of new, more sustainable plants, such as the INEOS cracker in Belgium, suggests ongoing opportunities for the development of bio-butadiene. To produce bio-butadiene there are a number of feedstocks which can be used to begin the process. The routes from these are depicted below:
Map of Alternative Bio-Butadiene Routes
Bio-Butadiene Historical Context
Butadiene was initially produced between the First and Second World Wars from acetylene via butanediols as intermediates by two routes, the Aldol process, and the Reppe process. These methods are no longer used, as the production of acetylene is energy- and capital-intensive. Further interest in butadiene rubber polymers, especially isoprene-butadiene comonomer rubbers led to development of processes based on ethanol, which were practiced in the United States, Russia, and Brazil. Although the technologies are proven and the investment cost is lower than other processes, higher operating costs, and low byproduct credits despite poor selectivity to butadiene make the process uneconomical and resulted in all plants in the United States closing in the 1950s.
How Things Have Changed
The focus of sustainability has shifted in the past decade to a carbon intensity based model, based upon the emissions resulting from the production of the product. Carbon Intensity, a relatively new concept to many in the petrochemical industry, is the measure of how much carbon dioxide equivalent emissions are released per unit of product (ton, MJ, or MWh, depending if it is a chemical, power, or fuel). This normalizes the emissions and makes sustainability efforts difficult to greenwash. Increasingly, many major market players including most international energy companies, chemical companies, and logistics and shipping companies have stated intentions of reducing their carbon intensity. A majority have even stated ambitions of net zero carbon emissions by 2050 and expect either a tax on carbon emissions or a credit for reductions. Increasingly, the financial sector is weighing carbon emissions in investment and are unwilling to fund what they see as ‘dirty projects’. Interest remains high for CI reductions for a few well joined premises:
We are limited by available renewable and sustainable materials and technologies: Simply put, there are not enough renewable feedstocks, renewable power, or renewable technologies available between now and 2050 to eliminate the use of fossil fuels and feedstocks. Even at very impressive industry growth rates—more than any previous industrial revolution—we will still likely fall short. Many will also need a way to offset otherwise uncapturable or ineliminable emissions;
Industry is expecting emissions regulation—and support for emission reduction technologies: Almost all major global multinational energy and chemical companies have publicly stated not only that they expect a carbon tax, cap and trade, and/or some other credit system to help curb emissions in major markets, but that they also support these efforts;
Consequences are stacking for inaction: It is now widely accepted that the global community will most likely not achieve the target of 1.5 degrees (or already has)—more powerful storms, raging fires, rising sea levels, droughts, and other disruptions to global food, chemical, and energy industries are rising with the mean temperature of the planet.
Around 95 percent of butadiene is produced as a co-product of the stream cracking process and is recovered via extractive distillation of the mixed C4 stream, the preferred method, since the relative volatilities of the various C4 isomers are such that they cannot be separated by conventional distillation. This means that the CI butadiene production is primarily a passenger to decarbonization of ethylene and propylene production (the main products of steam cracking). In order to take a driver’s seat in decarbonization, on-purpose low CI butadiene is required.
The Path Forward
Given the historical full commercialization of both the Coperbo and Lebedev processes, coupled with the fact that feed ethanol, the world's largest bio-based chemical, has experienced a consistent decrease in production costs and is rapidly advancing in commercialization from non-food sources, opting for either of these processes for bio-butadiene appears to be the lowest risk alternative. Both are about as attractive as any other alternative globally and are the most economically attractive in Asia. In a significant stride towards advancing upscale operations in the bio-butadiene industry, the BioButterfly™ partnership, comprising Michelin, IFP Energies Nouvelles, and Axens, marked a milestone in January 2024 by unveiling the inaugural industrial-scale demonstrator plant dedicated to butadiene production from bioethanol. With a production capacity of 20 to 30 tons per year, the plant marks a major step in securing major volumes of renewable butadiene. Synthos, alongside Lummus Technology, also have plans underway for a new 40 000 tons per year plant, commencing within the next 5 years. These historically relevant bio-butadiene technologies getting a second look are in good company, as several other “previously abandoned” technologies also getting second looks in light of new CI goals and focus. These include technologies and products such as cellulosic / advanced ethanols, methanol-to-gasoline (MTG, particularly with e-methanol), and algae-based carbon capture. The increasing value given to carbon intensity in the market place, combined with different market dynamics have made an opening in the market for renewably sourced, low carbon intensity, bio-based butadiene.
Find out more…
Biorenewable Insights Butadiene (2024 Program)
This report focuses on developments in the bio-butadiene industry sector. This includes routes from sugar, ethanol, BDO, CO, succinic acid, and butanol. Several technologies are profiled in this report:
- Direct Fermentation to butadiene as developed by:
- Geno
- Global Bioenergies
- Fermentation to BDO, followed by dehydration to butadiene, as developed by:
- Geno and Scientific Design for sugars feedstock, via 1,4 BDO
- LanzaTech and Invista for CO/syngas feedstock, via 2,3-BDO
- Geno, via 1,3-BDO
- Ethanol Butadiene
- The Lebedev process, a one-step conversion of ethanol to butadiene
- The Coperbo (AKA Ostermilinsky Reaction) a two-step conversion of ethanol to butadiene
- Processes with Feedstock Constraints and little progress in the market:
- Fermentation to succinic acid, hydrogenation of succinic acid to BDO, dehydrated to butadiene, as above.
- Sustainable Butadiene from Palm Fatty Acid Distillate
- Fermentation of Biomass to Butadiene
Cost of production models for USGC, Brazil, Western Europe and China are shown for butadiene from:
- Direct Fermentation of Sugars
- Sugar to BDO to Butadiene
- Carbon Monoxide to BDO to Butadiene
- Ethanol to Butadiene:
- Lebedev Process
- Coperbo Process
This report offers a catalogue of existing and planned renewable butadiene capacity and profile projects as well as analysis of the implications for conventional technology currently in the market, including the strategic implications.
Market Analytics: Butadiene - 2024
This report provides analysis and forecasts to 2050 of supply and demand of the global butadiene market. This analysis identifies the issues shaping the butadiene industry as well as provide detailed demand breakdown by derivative, supply and net trade data for 40 countries.
The Author...
Steve Slome, Principal
About Us - NexantECA, the Energy and Chemicals Advisory company is the leading advisor to the energy, refining, and chemical industries. Our clientele ranges from major oil and chemical companies, governments, investors, and financial institutions to regulators, development agencies, and law firms. Using a combination of business and technical expertise, with deep and broad understanding of markets, technologies and economics, NexantECA provides solutions that our clients have relied upon for over 50 years.