Blogs
February 24, 2025Crude oil to chemicals (COTC) The future of petrochemicals?
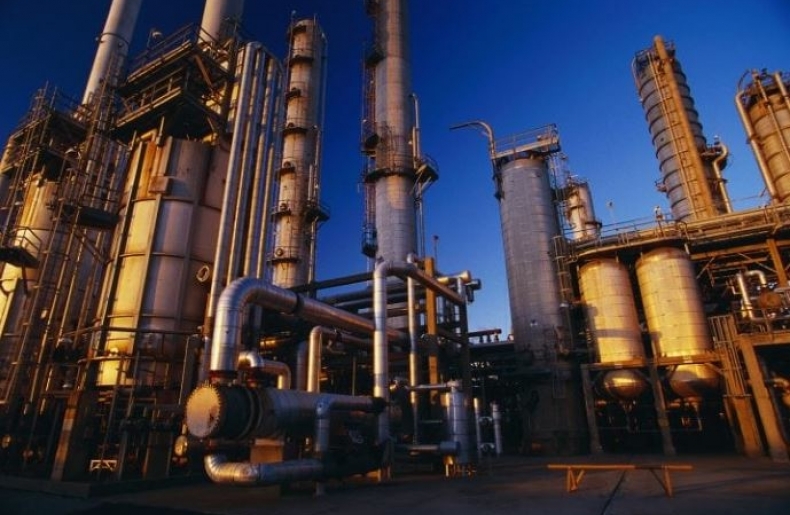
Higher Crude-to-Chemicals Conversion: A New Trend in Refining
In the early days of oil refining, crude oil underwent processing in basic refineries, where heavy residues were blended and sold as fuel oil. The refining of crude oil at the time focused on producing transportation fuels such as gasoline and diesel, with crude distillation and thermal cracking technologies to maximize these light products.
In the 1980s, accelerated growth of new materials and process development had increased demand for petrochemicals. Demand for products like synthetic rubbers and fibres re-focused refineries to increase their chemical yields. Complex refineries improved processing economics by upgrading fuel oil sales into higher value fuels such as gasoline, jet, diesel and petrochemicals.
Petrochemical yields are increased through integration of refinery and petrochemical plants:
- Moderate integration – Propylene extraction from Fluid Catalytic Cracking
- Medium integration – Aromatic extraction from gasoline
- High integration – Olefins steam crack from LPG and naphtha
With the improvement of hydrocracking and thermal cracking technologies, the presence of deep conversion refineries increased globally to reduce low value heavy refined products. As the demand for petrochemicals increased over the years olefins and aromatics integrated refineries gained popularity, mainly because refiners can better optimize their business operations between refined products and petrochemicals during the different market cycles.
In recent years increased adoption of renewable energy, and penetration of electrification of trains and vehicles reduces the growth of fuels, and fossil fuel demand is anticipated to peak in the mid-2030s. Declining fuel oil demand encouraged refineries to increase investment to further reduce or eliminate fuel oil by using more advanced technologies such as residue hydrocracking, residue FCCs or coking. Petrochemicals integration opportunities within these refineries are mainly created aromatics extraction from gasoline pool, or olefins production via FCCs or steam cracking of LPG/naphtha. As net zero ambition accelerates, fuels demand is expected to decline at a faster pace.
The demand for base chemicals such as olefins and aromatics is increasing. In 2023, NexantECA estimates that a total of 578 million tons of base chemicals is consumed. This number is anticipated to almost double by 2050. To meet the increasing petrochemicals demand while being increasingly focused on environmental concerns, the adoption of COTC technologies is becoming increasingly crucial.
Figure 1.1 Indicative Refinery Product Yields (wt%)
New COTC investments are more chemicals-focused, where NexantECA defines the two COTC phases as Phase One and Phase Two:
- Phase One COTC technologies can achieve petrochemical yields of 40 to 50 percent, typically by reconfiguring commercially proven technologies. Growing adoption of higher number of unit processes that converts crude oil to chemicals, particularly steam crackers. Existing refining facilities are retrofitted to include steam crackers and hydrocrackers to increase chemicals production.
- Phase Two COTC technologies may increase petrochemical yields up to 80 percent, by employing some developing technologies, some unproven at scale, while some may be technologically proven but not economically feasible. New grassroots refineries and expansion projects are being planned to handle crude oil directly with maximum naphtha and LPG production through cracking of medium and heavy streams. Naphtha and LPG products are then used as building blocks for petrochemicals in Phase Two COTC facilities.
Global COTC Investments: China Takes the Lead
Figure 1.2 COTC Investments in Asia Pacific and Saudi Arabia
Growing appetite in transitioning from fuels to petrochemicals has attracted almost US$ 120 billion in investments in COTC facilities globally, where more than 150 million tons per year of refining capacity either planned or operating. First notable COTC complexes are located in China:
- Zhejiang Petroleum and Chemical started operations in China in 2019 at Zhoushan, China. This has been expanded subsequently.
- Further Chinese investments by Hengli Petrochemical, Shenghong Petrochemical, and Shandong Yulong Petrochemical have exceeded US$ 60 billion.
In Brunei, Zhejiang Hengyi Group and the national Government’s Damai Holding has developed 160KBPD Hengyi Pulau Muara Besar (PMB) utilizing domestic crude oil to drive petrochemical exports to China. Phase II is due to start up in 2027 with approximately US$ 9 billion of investment.
South Korea’s S-Oil Ulsan facility features Saudi Aramco’s Thermal Crude to Chemicals (TC2C) technology with an estimated chemical conversion of up to 70 percent. In addition to the 46 KBPD crude oil capacity, this facility is also integrated with its existing refinery, using refinery naphtha and off gases into the new 1 800 thousand tons per year steam cracker, producing a variety of chemical products.
In Saudi Arabia, originally planned for a startup in 2025, Saudi Aramco and SABIC have delayed firm timings for COTC investments but are considering various projects. Commercialisation of the technology at S-Oil’s facility will be a key step.
Tabel 1.1 COTC Complexes in Operation or Planned
The Rising Importance of COTC
Latest technologies in COTC allows for refiners to opt for a higher production of base chemicals, meeting the higher petrochemicals demand in the next decade. As demand for traditional fuels weaken and global pledges towards carbon neutrality increases, refiners are starting to look towards COTC initiatives, as highlighted earlier.
Technology licensors had developed breakthroughs in technologies to convert heavy, low value residue streams in a refinery to naphtha, a key feedstock for olefins and aromatics production and integrated these technologies in their COTC offerings. These COTC offerings are typically proven technologies pieced together to maximize naphtha production. Often times, these new technologies have higher integration, where licensors claiming better cost optimisation through economies of scale, lower energy consumption through heat integration and lower carbon emissions.
The benefits of a COTC technology include the flexibility of opting for a mix of technologies or licensors. One such example being the Zhejiang Petroleum and Chemical project, which includes a mix of Honeywell UOP, Chevron and Eni licensed units in their 400 thousand barrels per day Phase I facility. Alternatively, refiners could opt for a more specialized, higher petrochemicals production technology such as the Honeywell UOP’s Naphtha to Ethane/Propane (NĒP) technology which is claimed to achieve up to 80 percent conversion to olefins.
Traditional COTC technologies are also flexible in their product yields. Zhejiang Petroleum and Chemicals had previously reduced their production of aromatics such as benzene and paraxylene production during a period of negative margins. In place of the reduction of aromatics production, the company increased their higher value diesel production for exports. These facilities offer adaptability to shift production between petrochemicals and fuels based on market demand, ensuring competitiveness in fluctuating economic conditions.
Find out more…
Market Analytics: Olefins - 2024
Market Analytics: Olefins - 2024 provides analysis and forecasts to 2050 of supply and demand of the global olefins market. This analysis identifies the issues shaping the olefins industry as well as provide detailed demand breakdown by derivative, supply and net trade data for 40 countries.
Market Analytics: Fuels and Feedstocks - 2024
This report includes discussion regarding key market trends, as well as supply, demand and trade analysis by region for the major refined products and NGLs, including:
• Market drivers (regulatory trends, macro-economic trends);
• Road fuel market drivers (vehicle fleet structure)
• Aviation fuel market drivers (Sustainable Aviation Fuel blend mandates and technology)
• Marine fuel market drivers (shipping decarbonisation, marine fuel diversification)
• Chemical feedstock use
Regions include North America, South America, Western Europe, Central Europe, Eastern Europe, Middle East, Africa, China and Other Asia Pacific.
The Author...
Jun Ying Liew, Analyst
About Us - NexantECA, the Energy and Chemicals Advisory company is the leading advisor to the energy, refining, and chemical industries. Our clientele ranges from major oil and chemical companies, governments, investors, and financial institutions to regulators, development agencies, and law firms. Using a combination of business and technical expertise, with deep and broad understanding of markets, technologies, and economics, NexantECA provides solutions that our clients have relied upon for over 50 years.