Blogs
July 29, 2024Global Polyolefin Elastomers and Plastomers market snapshot
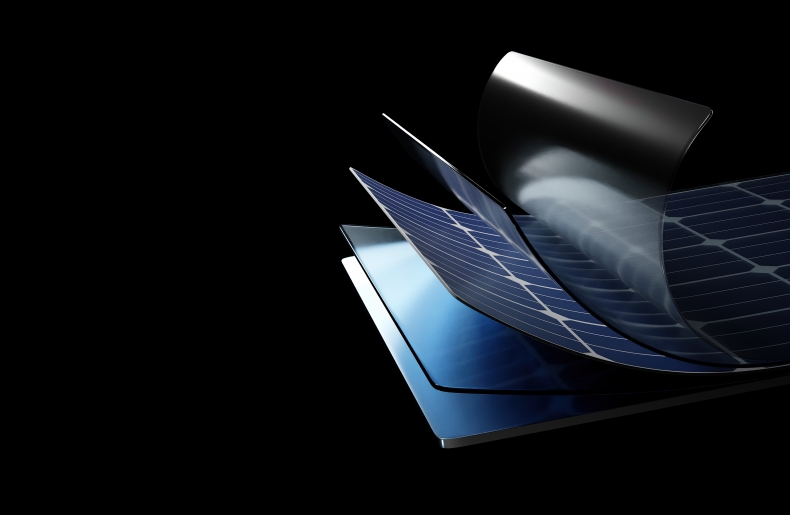
The ability of modern polyolefins production technology, particularly with metallocene catalysts, to produce ethylene-based materials with density below 0.915 g/cc has opened up commercial opportunities for a wide range of ethylene-based grades. In principle, materials as low as 0.855 g/cc or so (the theoretical minimum density for ethylene-based polymers) can be produced. There is no common nomenclature on what to call these materials, with the leading firms in this space having different terminology.
NexantECA uses the definition of Polyolefin Elastomers (POE) as having a density of 0.857 to 0.895 g/cc while Polyolefin Plastomers (POP) have a density in the range of 0.895 to 0.915 g/cc.
POE and POP based on ethylene typically contain about 65 to 85 percent ethylene and 15 to 35 percent octene-1, hexene-1 or butene-1, whether as a single comonomer or a combination of comonomers. With the exception of a few POP grades, all are produced via metallocene or constrained geometry catalysts. A metallocene catalyst is typically employed so as to achieve reasonable incorporation of the comonomer. Ziegler-Natta catalysts are sometimes used, but care must be taken so as to avoid excessive formation of low molecular weight species rich in comonomer which tend to be tacky and are an indication of poor heterogeneity of the comonomer. A more uniform incorporation of the comonomer in the polymer backbone results in a material with improved compression set, and thus improved elastomeric properties.
These materials are finding use as the elastomeric portion in compounded TPOs, or as polymer modifiers. All compounded TPOs were formerly PP/EPDM blends. However, POE have rapidly displaced EPDM, in most compounded TPOs. Some additional displacement of EPDM is projected on the basis of the ability to better tailor end-use properties (the POE are made with metallocene catalysts and thus their properties can be readily tailored), ease of handling (POE are in pellet form, whereas EPDM is typically baled), and lower overall cost (bales are more labour intensive to use than pellets). POE were also originally slated for use in improved flexible packaging films, though penetration into this application has been slow. Recently, POE have seen uses as low-cost rubber replacements for some non-demanding moulded goods applications - applications that will not be exposed to extremes in temperatures, pressures, loads or stress environments. In moulded goods, POE are being used where “some” degree of flexibility or tactile feel is desired.
Propylene-rich materials with some elastomeric properties have also been introduced in the past two decades. These are copolymers of propylene and ethylene or butene-1, with propylene content typically around 70 to 90 percent by weight, and ethylene or butene around 10 to 30 percent by weight. Note that there is less of an issue with nomenclature for propylene-rich materials since PP processes have been producing impact and random PP grades with significant ethylene content for decades. What differentiates the propylene elastomers from more traditional impact or random polymers is the use of metallocene catalysts to get more uniform and higher levels of ethylene comonomer into the polymer chains. This higher, relatively uniform ethylene incorporation results in an elastomeric material, different than a TPO where the ethylene is predominantly incorporated into the ethylene/propylene rubbery phase. Propylene-rich elastomers are finding use as impact modifiers and compatibilizers.
The key markets for the polyolefin elastomers are compounded TPOs, shoe soles and solar panel encapsulant films, while plastomers are used largely as is for films and extrusion coating applications.
Total global POE and POP demand is estimated at around 1.6 million tons in 2024, which includes ethylene-based and propylene-based elastomers but excludes OBCs.
Currently, the majority of POE demand goes into compounded TPOs, which accounts for about a quarter of the POE market. TPO applications that use POE include for example: acoustic barriers, appliances, audio tapes, automotive applications, battery cases, belts, cable jacketing, caps and closures, coatings, connectors, electrical parts, electronics, film, foam, gaskets, flexible grips, hose, household goods, industrial applications, insulation, electronic insulation, laminates, lawn and garden equipment, etc.
Compounded TPO in automotive is one of the major applications of POE. TPOs have been widely adopted for use in both exterior and interior automotive applications including bumpers, exterior parts, exterior trim, instrument panel, interior parts, interior trim, under-the-hood, and fascias. TPOs have been used as a replacement for more traditional materials, like metal, as well as engineering thermoplastics, such as acrylonitrile butadiene styrene (ABS) and polycarbonate (PC)/ABS. However, penetration of POE into compounded TPOs has slowed down, as some TPOs continue to require EPDM and EPR to reach the desired elastomeric properties.
PV encapsulant is the fastest-growing end-use for POE and the largest as of 2024. PV cell production has increased significantly in recent years due to the global push towards decarbonization and development of renewable energy. POE encapsulant is gaining market share due to its superior performance in high humidity and extreme weather condition and has greater induced degradation (PID) resistance compared to EVA encapsulant. This is evident in a bifacial PV module where both the front and back panels are made of glass. Acetic acid release from EVA is trapped in a glass-glass bifacial PV module causing corrosion and panel degradation while POE encapsulant does not release acetic acid when used in humid and wet condition. POE encapsulant also possess similar transparency as EVA, making it the better encapsulant material for bifacial glass-glass PV module. It is expected that POE encapsulant grows at a fast rate following the adoption of bifacial PV module that is more efficient than mono-facial module.
More than three quarters of the total POP consumption is in packaging. POP high toughness and tensile strength makes it a popular material for food packaging and industrial film. POP is typically compounded with polypropylene and polyethylene at about five to ten percent. This gives the packaging a better tensile strength and tear resistance. However, consumption growth in packaging has been slow as POP is normally priced at a premium over competing materials such mLLDPE and LLDPE.
POE and POP growth markets also include wire and cable, displacing PVC and to a lesser extent EPDM. There are a growing number of wire and cable applications requiring the use of halogen free or non-PVC insulation or sheathing materials. This has led to the growth of halogen free flame retardant formulations based on the use of ethylene copolymers and hydrated fillers. The use of POE and POP in the halogen free flame retardants formulation makes formulation more flexible and reduces hardness.
Not surprisingly, China is the largest single market for POE, followed by Asia Pacific (excl. China) and North America. China has large demand for POE due to the presence of a large automotive industry and PV manufacturing hubs. Growth is expected in the Middle East due to the rapidly growing infrastructure.
Global polyolefin elastomer capacity is estimated at around 3 million tons in 2024; although some of these facilities can swing to produce other products such as mLLDPE. POE and POP plants globally have been operating at high rates due to elevated demand supported to address increased PV production. However, with significant capacity addition expected in China, global operating rates are expected to decline in the medium term.
Find out more…
Market Insights: Polyolefin Elastomers and Plastomers – 2024
This report includes discussion regarding key market trends, as well as demand analysis by product and end use
- Polyolefin Elastomers (POEs): Polymer Modification, PV Encapsulant, Footwear, Wire & Cables, Others
- Polyolefin Plastomers (POPs): Packaging, Hot Melt Adhesives, Others
- in-situ Thermoplastic Olefinics (TPOs): Automotive, Building & Construction, Others
Regions include North America, South America, Western Europe, Central Europe, Eastern Europe, Middle East, Africa, China and Other Asia Pacific. Analysis also includes the competitive landscape, capacity listing, value chain development, and pricing and margin analysis by product and region.
About Us - NexantECA, the Energy and Chemicals Advisory company is the leading advisor to the energy, refining, and chemical industries. Our clientele ranges from major oil and chemical companies, governments, investors, and financial institutions to regulators, development agencies, and law firms. Using a combination of business and technical expertise, with deep and broad understanding of markets, technologies and economics, NexantECA provides solutions that our clients have relied upon for over 50 years.