Green steel and battery graphite
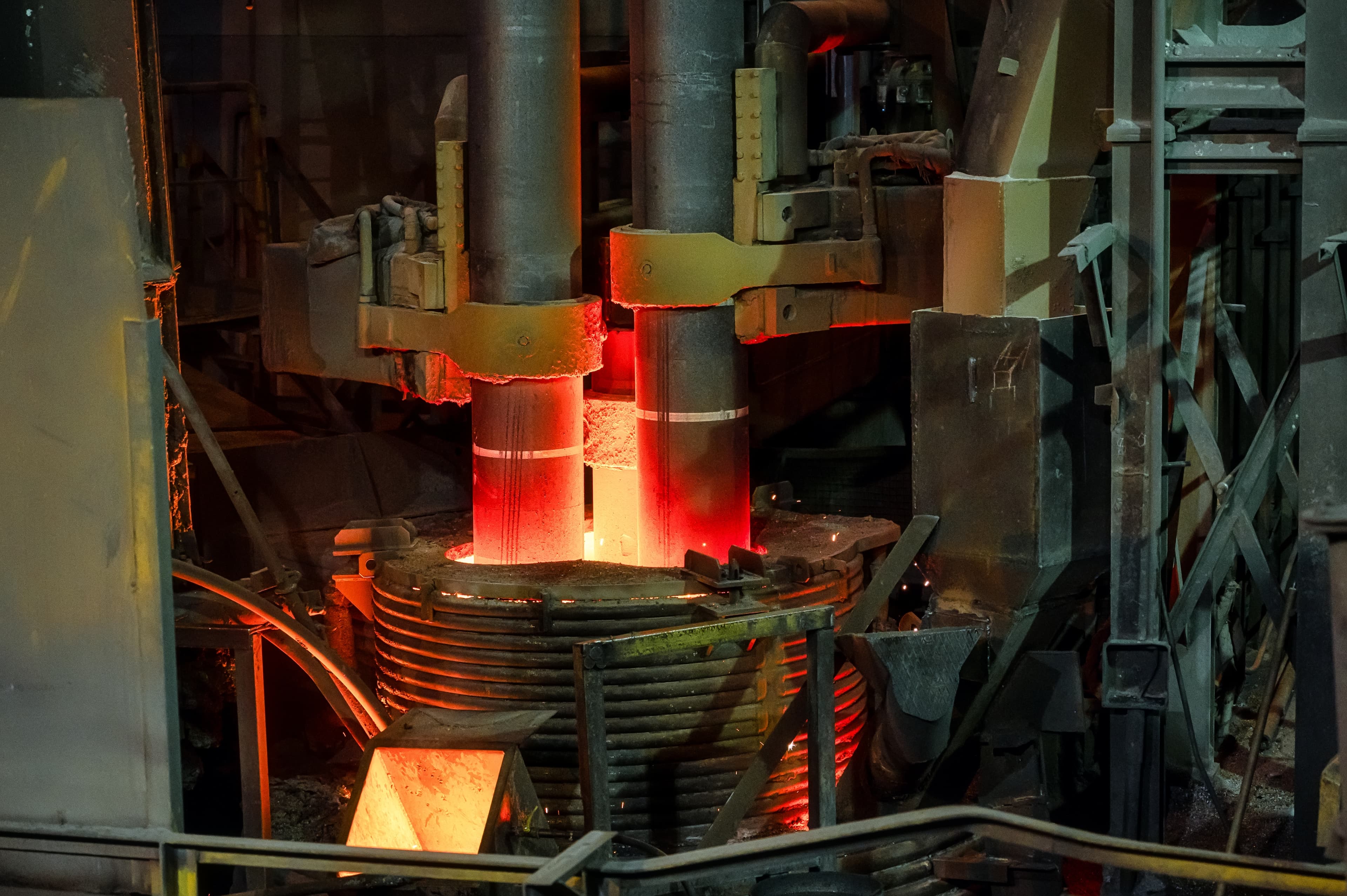
The world’s industries are going green. From steel to automobiles, ambitious public and private pledges along with tangible commitments have been made to produce net-zero carbon emissions industries by 2050. Moreover, environmental impacts are becoming increasingly valued beyond their climate change effects, with increasing initiatives to reduce metals, particulates, and sulfur emissions even in places that had previously shunned such concerns in favor of economic growth.
While the world’s automobiles have long since eschewed quarter-inch Detroit steel for their bodies, the greening of the steel industry has potential major supply chain effects on yet another critical material for automobiles: lithium-ion (Li-ion) batteries. While today’s battery-electric vehicle (BEV) market may be relatively small, major policy initiatives throughout the world have begun to push for the phase-out of internal combustion engines for personal transportation. Thus, Li-ion battery markets are expected to grow exponentially in the coming years, with new battery-electrics constituting 20 to 35 percent of sales by 2030. The connection between changing steel production methods and battery material supply chains become evident when looking at the complex value chain for graphite, a component used both in steel processing and, in highly specialized form, in Li-ion batteries.
Graphite is a structurally refined form of carbon that can be either mined from natural deposits or synthesized from a variety of petroleum and coal-derived feedstocks. Natural graphite has the advantage of low cost but grades that can used in applications such as batteries require expensive purification processes to be used effectively in electrochemical applications. Synthetic graphite is more expensive but can be produced in large and relatively uniform blocks at high purity for electrochemical use.
Graphite is used in steel as an electrode material, providing a high conductivity but relatively inert material for transmitting current for resistive heating to melt and process metals, and as a refractory material. Electrodes are continually consumed by the industry and require high purity and specified geometry, and are also consumed by foundry operations, albeit at a reduced level. Batteries also use graphite in an electrochemical capacity, as the key component of anodic material in a finished battery.
Recent developments in the greening of the steel industry and the impacts on the battery supply chain have been concentrated in China, the world’s largest center for both industries. 2019, in pursuit of its goal of peaking carbon dioxide emissions in 2030 and carbon neutrality by 2060, China began to push for changes in the highly emitting steel processing sector, which accounted for 15 percent of its annual domestic carbon footprint in 2020.
Among these changes were incentives for using steel scrap as a base feedstock – as opposed to the smelting of iron ore – as well as the shutting down of outdated production facilities and forcing production cuts from the peak in 2020. In terms of process technology, the net impact is to encourage greater use of processes that use graphite electrodes over those that use traditional fossil sources of energy such as coking coal, a goal shared around the world.
In the short term, the net result in 2021 was a massive boost in the use of arc furnaces and hot ladle processing in the world’s largest steel-producing country, which caused supply bottlenecks in synthetic graphite refractory and electrode materials. In addition, the shift away from basic oxygen processing of iron ore has resulted in similar crunch for much of the coal tar feedstocks used in graphite synthesis, which relied on coke ovens for production. This disruption as the second of a one-two punch: the graphite industry was already highly disrupted by the COVID-19 pandemic responses in China and elsewhere, as the heavy concentration of the graphite industry in China effectively halted most graphite processing worldwide in the second quarter of 2020, with financial ramifications up and down the supply chain.
Longer term, while the synthetic graphite industry will likely adapt to changing steel demand, the recent changes in China portend major shifts in graphite demand and have implications for Li-ion batteries. Ultimately, synthetic graphite remains driven by chemical metallurgy uses (not only in steel, but also in aluminum, chlor-alkali, and hydrogen production) that far outweigh battery uses in volume. These uses, already highlighted in the steel industry and hydrogen, are likely to continue expanding rapidly in response to current policy and industry trends. As a result, synthetic graphite will remain relatively expensive relative to historical levels.
Overall, green steel means the acceleration of current trends in battery graphite processing. Natural graphite in the last five years eclipsed synthetic graphite in Li-ion batteries due to the former’s lower cost and easily expanded mining, a trend that is likely to continue given surging synthetic graphite demand. However, natural graphite processing has its own specific issues. It has notably come under fire for the environmental and social impacts of its purification processes in China, and overseas manufacturers looking to move up in the value chain to battery-grade graphites have systematically pledged to not use the hydrofluoric acid-using hydrometallurgical purification that is currently prevalent.
Find out more...
Graphite and other carbon-based battery materials are covered in NexantECA’s 2021 TECH Report Advanced Carbon Materials in Lithium-Ion Batteries, part of NexantECA’s Technology and Costs Program. A study of the supply chain and processing of commoditized spherical graphite, conductive carbon black, and other advanced carbon materials used in lithium-ion batteries. Examines both natural graphite and synthetic graphite value chains as well as acetylene black. Strategic outlook for graphite is examined in the context of public policy for environmental protection from the perspective of climate change and fluoride pollution, as well as changes in supply chain, changes in battery technology, and battery-electric vehicles.
The Author
Joshua C. Velson, Consultant